Aluminum-Plastic Composite Film Seal Strength Testing Machine Vacuum Chamber Leak Tester For Packaging Beverage Bottle
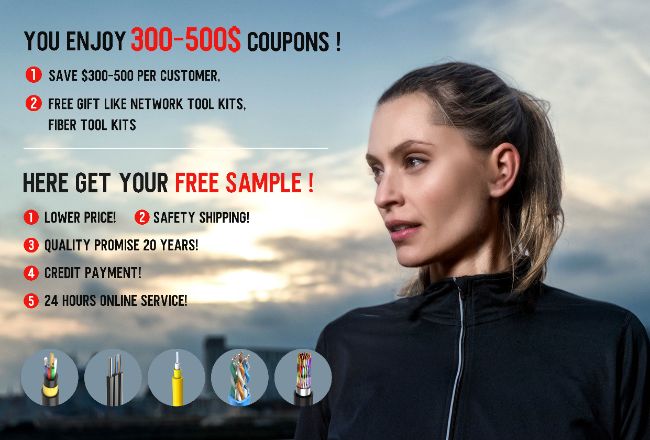
Contact me for free samples and coupons.
WhatsApp:0086 18588475571
Wechat: 0086 18588475571
Skype: sales10@aixton.com
If you have any concern, we provide 24-hour online help.
xAccuracy | 1% | Detection Range | 0~-90KPa |
---|---|---|---|
Dimensions | Φ270 X H210mm | Display | HMI Screen |
Name | Vacuum Leak Detector | Power Supply | Battery/AC |
Vacuum Measurement | Digital | Weight | 16kg |
Aluminum-Plastic Composite Film Seal Strength Testing Machine Vacuum Chamber Leak Tester For Packaging Beverage Bottle
Introduction to the Seal Strength Testing Machine
Ensuring the integrity and strength of packaging seals is crucial in industries such as food, pharmaceuticals, beverages, and medical packaging. A high-performance seal strength testing machine plays a key role in verifying seal integrity, preventing product contamination, and maintaining regulatory compliance. This machine evaluates the ability of a sealed package to withstand pressure variations, ensuring that the product remains safe during transportation, storage, and handling.
The seal strength testing machine provides accurate, repeatable, and reliable testing results, making it an essential tool for quality control and R&D in the packaging industry. This instrument is ideal for testing flexible and rigid packages, including pouches, blister packs, plastic containers, and composite films.
Why Seal Strength Testing Matters?
Packaging failures can result in product contamination, leakage, and reduced shelf life. A seal strength testing machine helps businesses:
-
Assess the durability of seals under varying pressure conditions.
-
Identify weak seals that could compromise product safety.
-
Optimize packaging materials and sealing parameters.
-
Comply with industry regulations such as ASTM F88 and ISO 11607.
Test Methods for Seal Strength Testing Machine
1. Precision Vacuum Leak Testing
The seal strength tester places the sample inside a transparent, water-filled vacuum chamber. The system then applies vacuum pressure to detect leaks through bubble formation. This test method ensures high precision in detecting micro leaks that are otherwise invisible to the naked eye.
2. Visual Confirmation of Seal Integrity
This test visually confirms leaks through the expulsion of air bubbles, pinpointing exact leakage points in packaging materials. By monitoring air escape, the system provides a clear assessment of seal quality.
3. Sample Expansion and Recovery
If no bubbles are observed, the sample’s expansion and recovery after vacuum release help determine seal integrity. This non-destructive test method allows manufacturers to assess packaging performance without damaging the sample.
Technical Features of Seal Strength Testing Machine
1. High-Precision Control System
Equipped with an advanced PLC-controlled unit, the seal strength testing machine ensures industrial-grade stability and reliability. The intuitive HMI touch screen provides an easy-to-use interface for test setup and data retrieval.
2. Venturi Tube Vacuum System
Unlike traditional vacuum pumps, this system utilizes a Venturi tube to achieve stable vacuum pressure up to -90KPa. The use of compressed air enhances efficiency and ease of operation.
3. Real-Time Data and Visual Analytics
The machine provides more than a simple pass/fail result. By recording cumulative test data and visual analytics, users can track performance trends and optimize production processes.
4. Multi-Parameter Memory for Testing Efficiency
The instrument allows users to save up to five different parameter groups, optimizing efficiency when testing various sample types. This feature enhances productivity by eliminating the need to reconfigure settings for each test.
Additional Features for Maximum Flexibility
-
Transparent acrylic chamber for clear observation of tests.
-
Customizable chamber sizes for testing different package dimensions.
-
Optional micro printer for direct test result documentation.
-
Multi-language display support for international applications.
-
Compatibility with vacuum pump systems for higher vacuum levels when required.
Main Technical Specifications
Parameter | Specification |
---|---|
Test Range | 0 to -90 KPa |
Chamber Material | Transparent Acrylic |
Chamber Size | Φ270mm x H210mm (Inside Usable) |
Power Supply | 110~220V, 50/60Hz |
Compressed Air Requirement | 0.7MPa (User Prepared) |
Chamber Options | Cylindrical and Cuboid |
Industries That Benefit from Seal Strength Testing Machines
-
Food Packaging – Ensuring airtight seals for extended shelf life.
-
Pharmaceuticals – Validating seal integrity in blister packs and medical pouches.
-
Beverages – Preventing leaks in bottle caps and flexible pouches.
-
Medical Devices – Ensuring sterile packaging remains uncompromised.
-
Consumer Goods – Assessing package durability for safety and convenience.
Why Choose Our Seal Strength Testing Machine?
-
High Sensitivity – Detects micro-leaks with precision.
-
User-Friendly Interface – Touchscreen operation with simple controls.
-
Reliable Data Recording – Stores test parameters for improved repeatability.
-
Customizable Options – Adaptable chamber sizes for different packaging needs.
-
Compliant with International Standards – Designed to meet ASTM and ISO packaging testing requirements.
Conclusion
A seal strength testing machine is an essential tool for quality control in packaging industries. It provides manufacturers with the confidence that their packaging can withstand real-world conditions, reducing the risk of product failure and improving customer satisfaction. By investing in a high-quality seal strength tester, businesses can ensure compliance with industry standards while enhancing product safety and reliability.