Vacuum Leak Tester By ASTM D3078 Method Vaccum Bubble Leak Testing Machine With Touch Screen
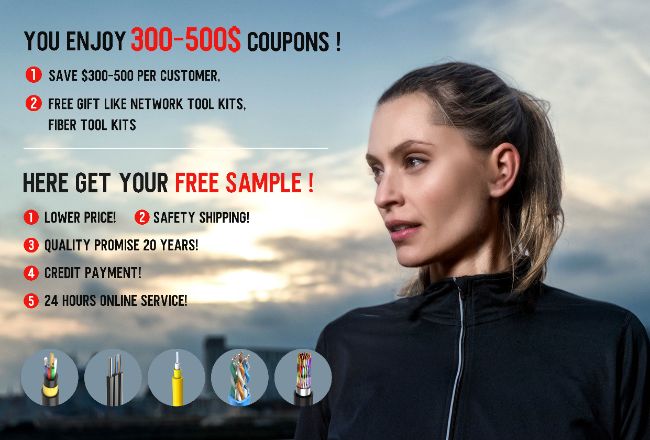
Contact me for free samples and coupons.
WhatsApp:0086 18588475571
Wechat: 0086 18588475571
Skype: sales10@aixton.com
If you have any concern, we provide 24-hour online help.
xAccuracy | 1% | Detection Range | 0~-90KPa |
---|---|---|---|
Dimensions | Φ270 X H210mm | Display | HMI Screen |
Name | Vacuum Leak Detector | Power Supply | Battery/AC |
Vacuum Measurement | Digital | Weight | 16kg |
Vacuum Leak Tester By ASTM D3078 Method Vaccum Bubble Leak Testing Machine With Touch Screen
Introduction to Vacuum Leak Tester
In industries such as packaging, food, medicine, and beverages, ensuring the integrity of package seals is paramount. The Vacuum Leak Tester is a cutting-edge instrument designed to accurately assess the sealing performance of various packages, ensuring that products remain protected from contamination, leakage, and external elements. By adhering to the ASTM D3078 standard, this vacuum leak testing machine provides a reliable, repeatable, and efficient method for detecting even the smallest leaks, safeguarding product quality and brand reputation.
Whether you're exploring sustainable packaging options, cost-effective alternatives, or fine-tuning production line parameters, the Vacuum Leak Tester plays a critical role in maintaining product quality and customer safety. With an advanced PLC-controlled system and a user-friendly HMI touch screen interface, this equipment ensures ease of operation without compromising precision or reliability.
The Significance of Vacuum Leak Testing
Vacuum leak testing is an essential step in the packaging process, particularly for products that must remain airtight. The Vacuum Leak Tester conducts tests by placing the sample inside a water-filled chamber. The process is meticulously designed to identify leaks by creating a vacuum environment. As pressure is reduced within the chamber, any breach in the packaging will be visually confirmed by the emergence of bubbles, pinpointing the leak’s location.
This visual confirmation is vital for industries where seal integrity is critical for product safety, such as pharmaceuticals, food packaging, and medical devices. By identifying potential weaknesses in packaging, manufacturers can make informed decisions about sealing processes, materials, and production parameters.
Key Features of the Vacuum Leak Tester
-
High Precision Vacuum Leak Testing The Vacuum Leak Tester initiates testing by placing the sample in a sealed chamber filled with water. Air is evacuated from the chamber until the preset vacuum level is reached. Any leaks are revealed by the appearance of bubbles, indicating the precise location of the breach.
-
Visual Leak Confirmation The visual nature of this test offers an easy-to-interpret result, where bubbles in the chamber visually confirm a leak’s presence. This method ensures both accuracy and simplicity, as operators can immediately identify where leaks occur and take action.
-
No Bubbles, No Problem In cases where no bubbles form, the Vacuum Leak Tester allows users to assess seal integrity by observing the sample's expansion and recovery. The equipment can detect subtle changes in the packaging, providing a comprehensive view of its sealing performance.
-
Built-In Intelligence for Efficiency The Vacuum Leak Tester is designed with a parameter-saving function for up to five different test groups, streamlining the testing process across multiple product lines. Operators can customize settings such as vacuum levels and test durations to fit specific product requirements.
-
Venturi Tube for Precision and Stability Using a Venturi tube for vacuum generation, this system achieves up to -90 KPa of pressure, offering precise and stable testing without the need for a vacuum pump. This design not only reduces maintenance but also enhances the accessibility of the equipment for industries requiring dependable, compressed air sources.
-
Adaptability and Customization The transparent chamber is built to standard sizes but can be customized to accommodate various shapes and sizes of packaging. This flexibility allows for the testing of a wide range of products, from small pharmaceutical blister packs to large beverage containers. Additionally, the system is compatible with optional vacuum pump configurations for those requiring higher vacuum levels.
-
Visual and Analytical Output Unlike standard pass/fail tests, the Vacuum Leak Tester provides numerical data that can be used for further analysis. This allows for detailed reports and a deeper understanding of the leak’s size and nature, helping industries improve their packaging design and sealing techniques.
-
Global Usability Designed for international use, the Vacuum Leak Tester offers multiple language display options, ensuring accessibility for global users. The default language is English, but other languages can be integrated to meet the needs of diverse operators.
-
Micro Printer for Record-Keeping For streamlined identification and record-keeping, the tester can be equipped with an optional micro printer, enabling users to print test results directly from the machine. This feature is particularly useful for laboratories and quality control departments that require documented evidence of testing.
Technical Specifications:
Test Range | 0~-90 KPa |
Chamber | Acrylic Cylinder Shape |
Test Space | Φ270*H210mm (Inside Usable) |
Compressed Air | 0.7MPa (Prepared by user) |
Power | 110~220V 50/60Hz |
Why Choose the Vacuum Leak Tester?
For companies involved in packaging, pharmaceuticals, food processing, and medical devices, maintaining seal integrity is non-negotiable. The Vacuum Leak Tester ensures that your packaging meets stringent quality standards, preventing contamination, ensuring freshness, and safeguarding against leakage. By integrating this machine into your quality control processes, you can reduce product recalls, enhance customer satisfaction, and comply with industry regulations.
Moreover, the Vacuum Leak Tester is a versatile tool that can be customized to meet your specific testing needs. From small, delicate packages to large containers, this equipment ensures accurate results across a broad range of products. Whether you're testing flexible films, rigid containers, or complex packaging structures, the Vacuum Leak Tester delivers the precision and reliability your industry demands.
Key Benefits for Industry Applications:
-
Packaging Industry: Ensure package integrity and prevent leakage in food, beverage, and pharmaceutical products.
-
Pharmaceutical Industry: Maintain sterility and protect sensitive medications from contamination through rigorous leak detection.
-
Food Industry: Guarantee freshness by detecting potential leaks in vacuum-sealed and modified atmosphere packaging.
-
Medical Devices: Test the seal integrity of medical packaging to meet stringent regulatory standards.