Heat Seal Test Apparatus Polyer Film Heat Sealer Lab Use
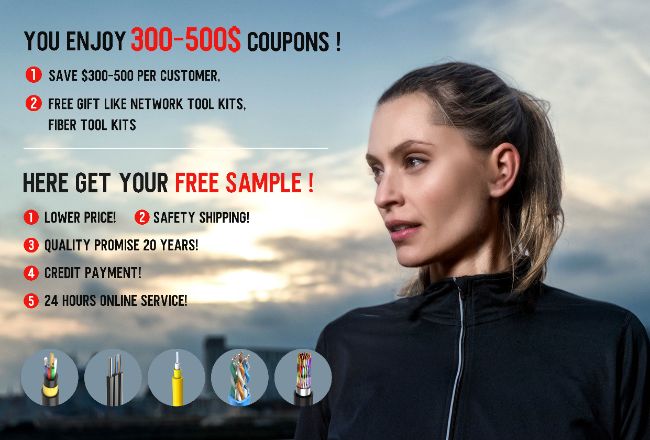
Contact me for free samples and coupons.
WhatsApp:0086 18588475571
Wechat: 0086 18588475571
Skype: sales10@aixton.com
If you have any concern, we provide 24-hour online help.
xHighlight | heat seal,Laboratory,testing |
---|
Heat Seal Test Apparatus Polyer Film Heat Sealer Lab Use
Sealing Temp. | Ambient~300℃ |
Deviation | ±0.2℃ |
Sealing Time | 0.1S~9999S |
Sealing Pressure | 0.15~0.7 MPa |
Seal Jaws | 330*10 mm L*W |
Gas Pressure | 0.7 MPa |
Port Size | Ф6 mm PU Hose |
Power | AC 220V 50Hz |
The Heat Seal Test apparatus is a specialized instrument designed to help laboratories, manufacturers, and researchers accurately evaluate the sealing performance of various packaging materials. This device is essential for determining the optimal sealing parameters, including temperature, time, and pressure, to ensure that materials such as films, laminates, composites, and polymers achieve the best possible heat-sealed performance. Whether you're working in the food, pharmaceutical, beverage, or packaging industry, the Heat Seal Test apparatus offers reliable data to enhance your product quality and meet industry standards.
What is the Heat Seal Test Apparatus?
The Heat Seal Test is an essential procedure for evaluating the heat sealability of flexible packaging materials. Heat sealing is a critical process in industries such as food and beverage, pharmaceuticals, and consumer goods, as it ensures product integrity, safety, and shelf life. The Heat Seal Test apparatus is designed to simulate production sealing conditions in a controlled environment, allowing companies to optimize their sealing processes and produce packaging that meets stringent quality requirements.
This versatile testing instrument is designed for use in quality control labs, research facilities, and production lines, offering detailed insights into how materials behave under different sealing conditions. With customizable sealing jaws, independent upper and lower jaw heating, and precise control of temperature, dwell time, and pressure, the Heat Seal Test apparatus is the ultimate solution for sealing performance testing.
Key Features of the Heat Seal Test Apparatus
-
Five Sealing Temperatures in One Test: The Heat Seal Test apparatus can evaluate up to five different sealing temperatures in a single test cycle, streamlining the process and providing a comprehensive understanding of how materials perform under varying conditions.
-
Precise Dwell Time and Pressure Control: The apparatus includes proximity and pressure sensors that ensure accurate control of the sealing process, reducing variability and ensuring consistent results.
-
P.I.D. Temperature Control: Equipped with Proportional-Integral-Derivative (P.I.D.) technology, the Heat Seal Test apparatus maintains precise control over the sealing temperature, eliminating fluctuations that could affect the test outcomes.
-
Uniform Heating Across Sealing Jaws: The aluminum-encapsulated sealing jaws provide uniform heating, ensuring that no inhomogeneous heating affects the sealing quality. This uniformity is critical in ensuring that seals are consistent and strong across the entire material surface.
-
Independent Upper and Lower Jaw Heating: The Heat Seal Test apparatus offers independent heating for the upper and lower sealing jaws, enabling users to test multi-layer materials and customize heat application for each layer of the sample.
-
Customizable Sealing Jaws: This apparatus is designed with flexibility in mind. Users can customize the dimensions, shape, and surface of the sealing jaws to accommodate different material types and test specifications.
Applications of the Heat Seal Test Apparatus
The Heat Seal Test apparatus is widely used in industries that require reliable packaging solutions. Some key industries and applications include:
1. Food Packaging
Food products rely heavily on secure seals to maintain freshness, prevent contamination, and extend shelf life. The Heat Seal Test apparatus allows manufacturers to test and optimize the heat sealing parameters for a variety of packaging materials such as polyethylene, polypropylene, and multi-layer laminates. Accurate testing ensures that the packaging material can withstand different production environments and storage conditions.
2. Pharmaceutical Packaging
In the pharmaceutical industry, secure seals are vital for maintaining product safety and efficacy. Packaging materials used for pharmaceutical products must meet strict regulatory standards to ensure that they can preserve the integrity of the contents. The Heat Seal Test apparatus helps pharmaceutical manufacturers evaluate the heat sealability of blister packs, vials, and medical-grade films, ensuring compliance with regulatory requirements.
3. Beverage Packaging
Beverage containers, especially flexible pouches, need to be sealed tightly to prevent leakage and contamination. The Heat Seal Test ensures that the sealing parameters are precisely controlled, delivering durable seals that protect the product from external elements while maintaining the quality of the beverage.
4. Medical Device Packaging
Medical device packaging requires stringent testing to ensure sterility and prevent contamination. The Heat Seal Test apparatus is used to evaluate the heat sealability of sterile barrier systems, ensuring that the materials can maintain a secure seal throughout the product's lifecycle.
5. Consumer Goods Packaging
From cosmetics to household products, consumer goods packaging must provide secure seals to protect products from damage, leakage, or tampering. The Heat Seal Test apparatus allows companies to fine-tune the sealing process for plastic films, laminates, and other flexible materials, ensuring that packaging meets consumer expectations and industry standards.
How the Heat Seal Test Works
The Heat Seal Test process involves applying controlled heat and pressure to a test material for a specified amount of time. The goal is to simulate the sealing conditions used in actual production environments to determine the material's heat sealability.
Using the Heat Seal Test apparatus, users can adjust the following parameters to ensure optimal seal quality:
- Sealing Temperature: By varying the temperature applied to the material, users can determine the ideal sealing temperature that produces a strong, durable seal without damaging the material.
- Dwell Time: This refers to the amount of time that heat and pressure are applied to the material during the sealing process. The Heat Seal Test apparatus allows for precise control of dwell time, ensuring consistent results.
- Pressure: The pressure applied during sealing affects the integrity of the seal. Too much or too little pressure can result in weak or incomplete seals. The Heat Seal Test apparatus includes sensors to ensure that pressure is applied uniformly and accurately.
Standards Compliance
The Heat Seal Test apparatus is built to comply with international standards for heat sealing testing. This ensures that your testing processes meet industry best practices and regulatory requirements. The relevant standards include:
- ASTM F2029: A widely recognized standard that outlines the test method for determining the heat sealability of flexible barrier materials.
- QB/T 2358: A Chinese standard that specifies the technical requirements for heat seal testing.
- YBB 00122003: A standard commonly used in medical packaging to evaluate the sealing performance of materials.
Why Invest in a Heat Seal Test Apparatus?
Investing in the Heat Seal Test apparatus provides several key benefits for manufacturers, quality control labs, and research institutions:
- Increased Efficiency: By testing multiple sealing parameters in one cycle, the apparatus saves time and improves workflow efficiency.
- Improved Product Quality: Accurate sealing ensures that packaging materials maintain their integrity, reducing waste and product recalls.
- Cost Savings: Optimizing sealing parameters can lead to significant cost savings by reducing energy consumption, material waste, and production errors.
- Regulatory Compliance: Meeting industry standards for heat sealing ensures that your products are compliant with relevant regulations, reducing the risk of fines or product recalls.
- Versatility: With its customizable sealing jaws and independent heating controls, the Heat Seal Test apparatus can handle a wide range of materials and applications, making it a valuable asset for companies with diverse packaging needs.
Maintenance and Calibration
For optimal performance, regular maintenance and calibration of the Heat Seal Test apparatus are essential. This includes routine checks of the heating elements, pressure sensors, and sealing jaws to ensure consistent results. Calibration should be performed according to the manufacturer's guidelines to maintain accuracy and compliance with industry standards.
Conclusion: The Importance of the Heat Seal Test in Packaging
The Heat Seal Test is a critical component of packaging quality control. Whether you're producing food packaging, pharmaceutical products, or consumer goods, ensuring that your materials are properly sealed can prevent product loss, contamination, and customer dissatisfaction. The Heat Seal Test apparatus provides precise, reliable data to optimize your sealing processes, helping you meet industry standards and maintain the highest levels of product integrity.